The Best in Logistics
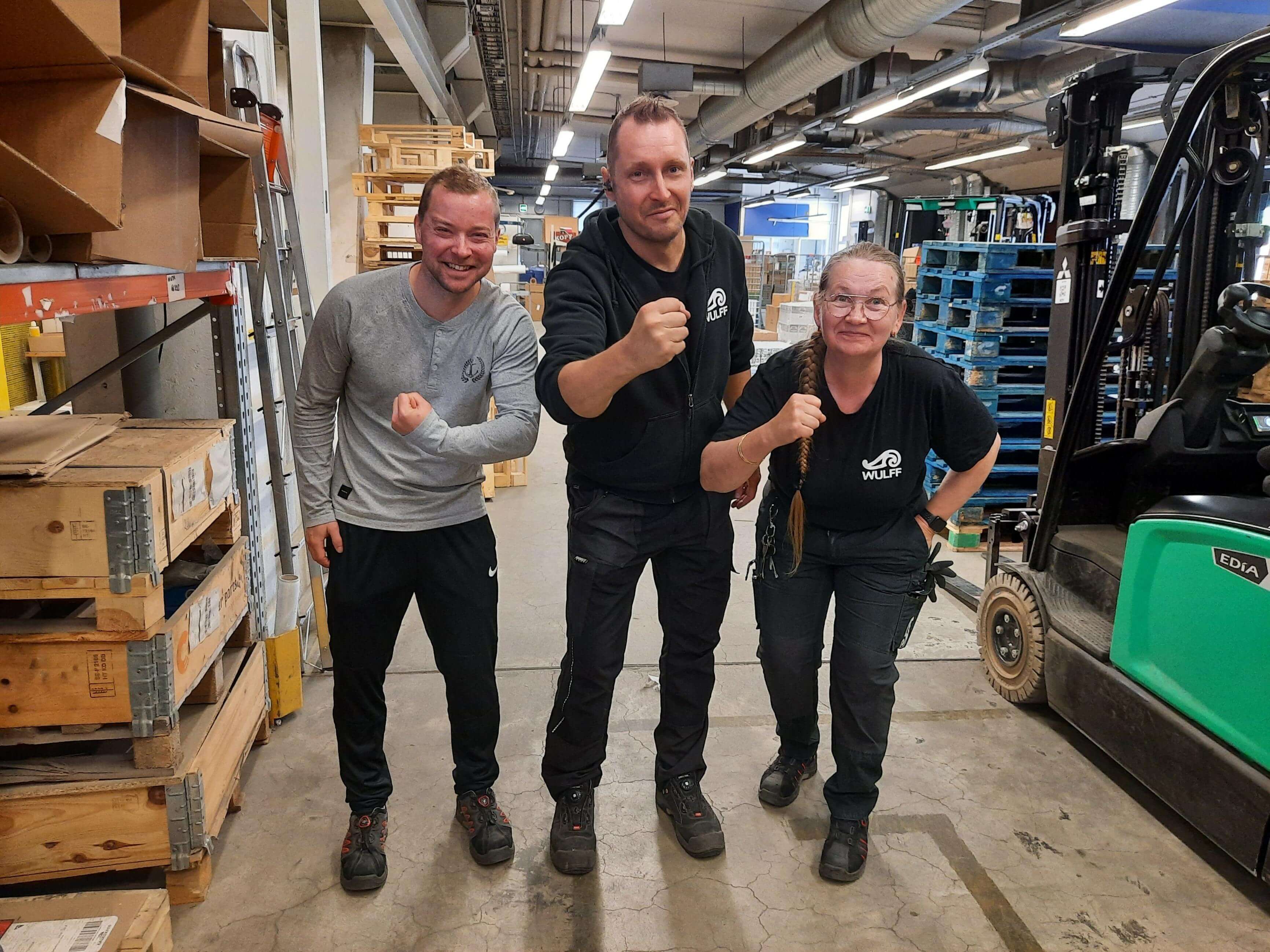
What does effective and service-oriented logistics look like? At Wulff, we utilize artificial intelligence and picking robots – and at the heart of it all is our skilled and caring staff! In this article, you'll get an inside look at Wulff's logistics center in Tuusula and its operations.
When discussing logistics with customers, Wulffians often fondly refer to Pakkasraitti. From Pakkasraitti in Tuusula, you'll find a vital space for Wulff buzzing from morning to night: a modern logistics center where top-tier technology is leveraged, and work is propelled by technology in two shifts.
In addition to our Tuusula center, Wulff also operates its own logistics in Espoo's Kilo at the Wulff House, which also houses Wulff's Nordic headquarters. The Espoo logistics center serves Wulff's Expertise Sales. In Tuusula, the focus is on the logistics for Wulff's Contract Sales customers, with additional support from a logistics center in Akaa, managed in collaboration with Posti. Altogether, our staff and robots collect around 1.2 million order lines of products annually. The most important goal every workday is to ensure that orders are accurately picked, and shipments are swiftly sent to customers.
”We excel at meeting this goal,” says Marko Helin, Wulff's Development Manager responsible for logistics, with a satisfied smile. ”The industry often talks about the error-free percentage of deliveries. Ours has been 99.9% for years. You could call it a 'perfection percentage',” Helin suggests.
Perfectly picked orders save customers' time, whether it's products for workplace use or items destined for a reseller's sales shelf. Warehouse Manager Jussi Penttilä elaborates through customer feedback: ”When you see a shipment from Wulff, you know there's no need to follow up on product exchanges or missing items – such feedback warms the heart.”
Jussi Penttilä, along with foremen Päivi Virtanen-Gill and Juha Julkunen, have all worked at Wulff's Tuusula logistics center since its opening in 2006. As logistics and development professionals, they steer a 30-person expert team with determined yet gentle guidance.
The super-efficient logistics center owes its prowess to the combination of artificial intelligence, robotics, and human labor. ”A significant part of the picking is done automatically. Robots traveling along long corridors lift boxes destined for customers onto logistics systems controlled by automation. People still play a role in this automated logistics world. For instance, when picking smaller quantities of products and individual items, opening boxes and picking products from packing pallets require the nimble and professional touch of a Wulffian,” Virtanen-Gill explains the practical operation.
”Sometimes the machine still comes second, and that's okay. Plus, even the machines need support and maintenance from time to time,” Julkunen clarifies. ”We've built and set up this entire system ourselves, so here the machine still obeys the human, not the other way around,” Penttilä jokes alongside.
A positive customer experience is built on well-managed and efficient logistics
Sustainability and zeroing emissions are of interest
At Wulff's Tuusula logistics center, environmental responsibility is considered in many ways. Solar panels installed on the roof collect energy that is used to power the logistics center. Interesting details are also found in waste recycling. For example, all recyclable plastics are collected and sent for reuse, such as granulate. Orders are packed in recycled cardboard boxes whenever possible. Clean boxes suitable for reuse get a ”I've been recycled” sticker, informing the recipient of the good deed and choice.
Waste heat becomes useful heat!
The logistics center employs compressors that repurpose waste heat by blowing warm air into the dispatch area and thus into the ventilation system. ”With the fan, we can direct warm air from one floor to another, and we can use the already heated air through ventilation recovery,” explains Penttilä. This significantly reduces energy consumption.
Wulff's ethos is that when a customer orders comprehensively from one partner's selection for all their work and workplace needs, this business model in itself reduces the number of deliveries and emissions to the customer's site. When procurement is further optimized for the right time frame—often shifting from weekly orders to monthly with a bit of planning—the real emissions from deliveries are significantly reduced. Delivery partner Posti handles Wulff's deliveries in a carbon-neutral manner. Posti offsets all the necessary emissions from Wulff's deliveries into certified climate projects.
Acquisitions catalyzing growth and advancements in logistics operations
We conducted interviews for this blog during the peak school supply season of spring 2023. ”In three weeks, we send out over 20,000 lines of school supplies, in addition to our daily 3,000 lines,” say Wulff's logistics experts.
The increase in the number of products picked and delivered isn't just a seasonal phenomenon. The growth in shipped products is not expected to be just a seasonal trend. Julkunen, Penttilä, and Virtanen-Gill look forward to the fall of 2023 with great anticipation. It brings changes and, above all, opportunities, as the production volume of Wulff's Tuusula logistics center is set to increase significantly. Following the acquisition of Staples Finland Oy in spring 2021, companies have been merged and various operations integrated. The number of items is growing by several thousand. ”It's exciting and inspiring to grow into Wulff's main warehouse for Contract Sales. Now we're focusing on how we can continue to improve our operations to ensure that everything continues to work well and as efficiently as possible. There's always room for innovation and to learn more,” summarizes the spirited logistics center team.
Interested in a tour of the Logistics Center?
We offer guided tours. Arrange a visit by contacting Warehouse Manager Jussi Penttilä at jussi.penttila@wulff.fi.